- Published on
Multiphase flow in Hydrophobic Meshes: Comsol model and app
- Authors
Author
- Name
- Emilie Coenemail
Background
Accidental oil spills in aquatic environments are a recurring problem in the oil and gas industry and have severe ecological, social and economic consequences.
There are several oil spill clean-up techniques, such as skimming, in-situ burning, biodegradation, hydrophobic meshes, etc. Hydrophobic meshes are generally made of stainless steel and coated with a hydrophobic and oleophilic material. They act as a filter: the oil passes through the mesh, while water is retained outside.
Hydrophobic meshes are still at an early development stage but offer many advantages: they are clean, can be operated continuously, require low energy input, present good recovery capacities and recover pure oil, which allows to recycle the spilled oil. The only disadvantage is the operation depth: when a hydrophobic mesh is submerged below its breakthrough pressure depth, water will intrude and contaminate the recovered oil.
Conceptual Model
The model presented here conceptualizes a hydrophobic mesh as a porous medium. The model is based on the black oil model, which is extensively used for oil reservoir simulations, and solves multi-phase flow in porous media. In this case there are two phases: water and oil (air was not included in the model).

The governing equations consist on a system of two partial differential equations, one for each phase.
Oil Mass Balance:
Water Mass Balance:
The system of equations is solved for the water pressure, Pw, and the capillary pressure, Pc. is the porosity of the mesh, So the oil saturation, k the permeability of the mesh and λw and λo refer to water and oil phase mobilities, respectively. The porosity and permeability depend on the dimensions of the mesh, which are the coated wire radius and pore radius. The phase mobilities depend on fluid properties and retention properties of the mesh.
Implementation in Comsol
The model was implemented in Comsol Multiphysics using a 1D geometry and the coefficient form PDE interface.
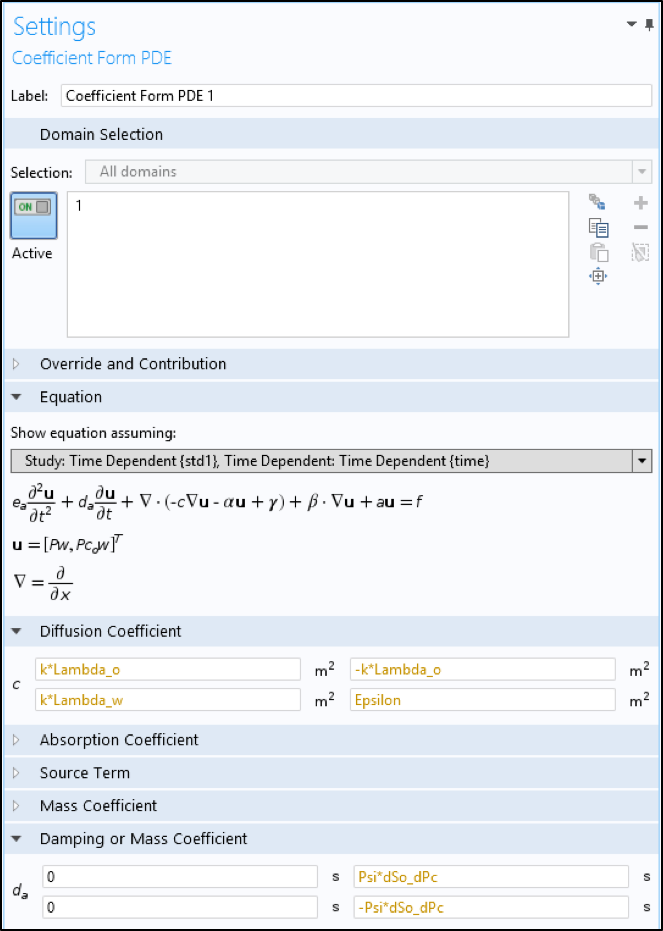
The water and capillary pressures were defined at the boundaries with Dirichlet boundary conditions. The initial condition in the mesh is full oil saturation.
In the Figure below, one can see the typical behavior of a hydrophobic mesh. At low depths there is only oil flowing through the mesh, with higher fluxes at higher depths, until the breakthrough pressure is reached at a depth of 0.7 m. Then the water flux increases, contaminating the recovered oil.
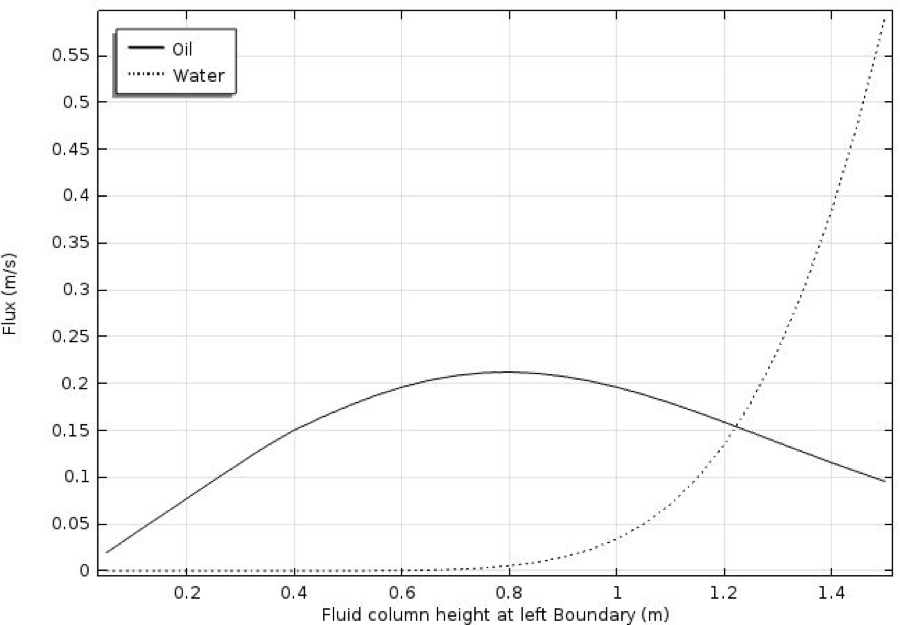
App development with Comsol Application Builder
Once the Comsol model was developed, the Comsol Application Builder feature was applied to create a practical and user-friendly tool tailored for mesh designers and/or operators.
The App allows the user to set the main parameters that define the system, such as mesh, oil and water properties, and retention function parameters.

Once the parameters are introduced, analysis of the mesh can be facilitated through different studies e.g. breakthrough and pore analysis.
The “Breakthrough Analysis” window allows to determine the depth at which water breakthrough occurs. Oil and water fluxes, oil saturation and water fractional flow can be obtained following the definition of pore radius of the mesh and operational depth interval.
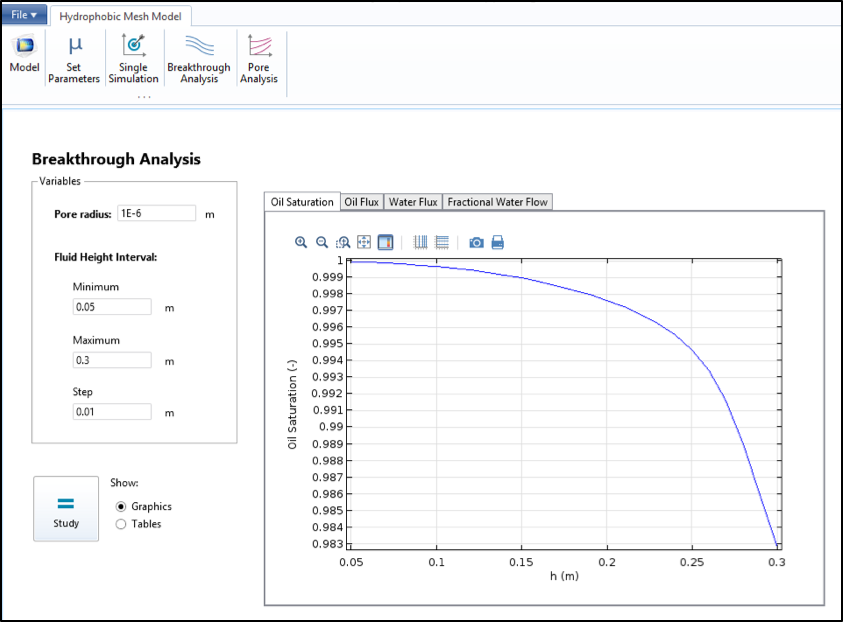
The “Pore Analysis” window, on the other hand, can be used to determine an optimum mesh pore radius. Wider mesh pores enhance both water content and oil fluxes. Hence, the optimum mesh size must be chosen in such a way to maximize oil flux while maintaining a low water content. In this window one can compare both variables for a set of depths and pore radiuses.

Summary and Conclusions
Hydrophobic meshes offer many advantages when it comes to oil spill clean-ups. This project shows that these meshes can be modelled as porous media with multiphase flow.
The model offers a good understanding of how these meshes work, and can be a useful tool for researchers, designers and users.
Acknowledgements
This project has been made possible thanks to the CRUE-CEPYME scholarship of Banco Santander. I would like to express my gratitude to Orlando Silva and Jorge Molinero for the help received during this project.
References
[1] COMSOL Multiphysics. COMSOL Multiphysics® Reference Guide Version 5.1; COMSOL AB: 2015.
[2] COMSOL Multiphysics. Introduction to Application Builder Version 5.0; COMSOL AB: 2014.
[3] Deng, D., Prendergast, D.P., MacFarlane, J., Bagatin, R., Stellacci, F., Gschwend, P.M. (2013). Hydrophobic Meshes for Oil Spill Recovery Devices. Applied Materials and Interfaces 5 pp. 774-781.
[4] Diaz-Viera, M.A., Lopez-Falcon, D.A., Moctezuma-Berthier, A., Ortiz-Tapia, A. (2008). COMSOL implementation of a multiphase fluid flow model in porous media. Proceedings of the COMSOL conference 2008 Boston.
[5] Song, J., Huang, S., Lu, Y., Bu, X., Mates, J. E., Ghosh, A., ..., Megaridis, C. M. (2014). Self-Driven One-Step Oil Removal from Oil Spill on Water via Selective-Wettability Steel Mesh. Applied Materials and Interfaces 6 pp. 19858-19865.